Air filter devices and applications
Mechanical and electrostatic air filter devices for industrial air pollution control
Air filter devices from ISI Industrieprodukte GmbH are used to separate oil mist, emulsion mist, smoke and other aerosols.
Welcome to ISI Industrieprodukte GmbH. As a manufacturer of industrial air filter systems for machine tools, we have been dedicated to the operational environmental and health protection of your employees for over 50 years.
Our ELBARON®, COBARON and TEBARON series have been the industry standard for electrostatic and mechanical technologies for industrial air purification since 1973.
Applications
for mechanical and electrostatic air filter devices
Basically, we distinguish between the following applications in the design of our industrial air cleaners:
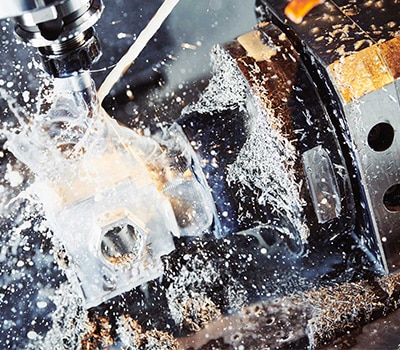
Oil/emulsion mist
Oil/emulsion mist with smoke development. During heavy-duty machining with oil or emulsion (with more than 5% oil content), oil or emulsion mist with smoke development occurs due to the high process temperatures. Smoke in particular is difficult to filter due to its very fine particles.
Our solution
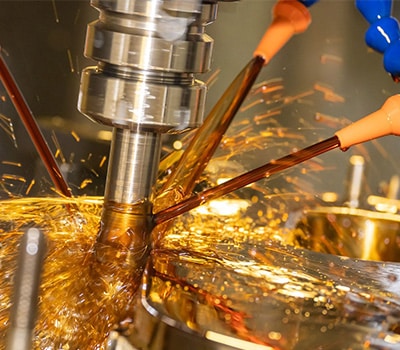
Oil mist
Oil mist is generated during machining with pure oil as a cooling lubricant. Oil mist is a large quantity of airborne, very fine oil droplets which are produced during turning, milling, drilling or grinding with oil and during dry machining with MQL (minimal quantity lubrication quantity).
Our solution
The ISI filter device series– High production quality & tried-and-tested technology
Savings potential and benefits that can be realized by using air filter devices from ISI Industrieprodukte GmbH
Increase environmental & health protection
Our filter units capture the pollutants at their point of origin and release the cleaned air into the environment as exhaust air (separation efficiency 99.95% for mechanical filters with HEPA filters). Without a filtration concept, these pollutants are released into the environment and can pose health risks to your employees.
Reduction of operating costs
Thanks to our modern ISI-Tronic control technology, only the minimum amount of energy required in the filtration process is used. This economical operation of our unit series is made possible by continuously variable, highly energy-efficient EC fans. This guarantees sustainable and economical operation of your systems.
Reduction of ancillary costs
Due to the high, continuous separation efficiency, our filter systems can be operated in recirculation mode. The machine exhaust air does not have to be led outside, but remains purified in the production hall. This improves the energy and heating cost balance.
Reducing cleaning costs
Machine controls are sensitive to contamination by oil mist and fine dust. Increased cleaning and repair costs are the result. This also applies to other electronic or mechanical operating equipment. Filter devices from ISI prevent this problem from arising in the first place and ensure a clean working environment.
Long service life
Due to our high-quality materials and manufacturing processes, our air filtration units have very long service lives. Filter media can be easily replaced or cleaned and are therefore not only more cost-effective in the long run, but also a plus for your personal eco-balance.
Air filter devices from ISI | Technology that convinces
Energy efficiency and cost-effectiveness play a important role
All ISI device series are characterised by high manufacturing quality and field-proven technologies. We attach great importance to proven functionality and digitalised control technology.
Industrial air pollution control has never been as transparent, plannable, and economical as by using an air filtration unit with ISI-TRONIC.
You will receive almost all of our filter unit series with our digital filter unit control ISI-TRONIC as standard. With ISI-TRONIC, you can monitor and evaluate all processes in the filter unit centrally via the company network, with a laptop or your smartphone directly at the machine, or with our ISI-TRONIC CONTROL accessory device.
In addition, all our filter systems operate with a highly efficient EC fan. Through the consistent use of economical EC fans, energy savings of up to 60% compared to conventional three-phase fans can be realistically implemented.
With these advanced solutions, you not only comply with the applicable environmental regulations, but you also make an active contribution to protecting the health of your employees by creating a safe and clean working environment.
By taking into account ongoing trends and legal requirements in the field of environmental and health protection, you position your company as a responsible market player and at the same time secure competitive advantages through innovative technologies.
Industrial air filter devices from ISI Industrieprodukte GmbH
Close to the customer and in tune with the times
The continuous communication between our sales team and our technical department, and therefore between the market and the manufacturer, ensures that changing market requirements are incorporated into new technical developments. This enables us to develop needs-based solutions with well thought-out details.
When further developing our technology, we always focus on the benefits and added value for our customers in order to position our products on the market in the long term.
Issues such as energy efficiency and cost-effectiveness are fundamental aspects that play a decisive role in the further development of our technology.
In addition to working on completely new developments and constant improvements to existing appliance series, our ongoing quality assurance is of course constantly being perfected.
All devices are subjected to a comprehensive function and quality test before dispatch. The resulting data is logged and permanently archived. This ensures error-free commissioning and reliable operation of our filter devices.
ISI-Group – Your contact persons
At the ISI Group, we see ourselves as partners to our clients and place great importance on individual consultation to achieve top-notch results in the field of air purification.
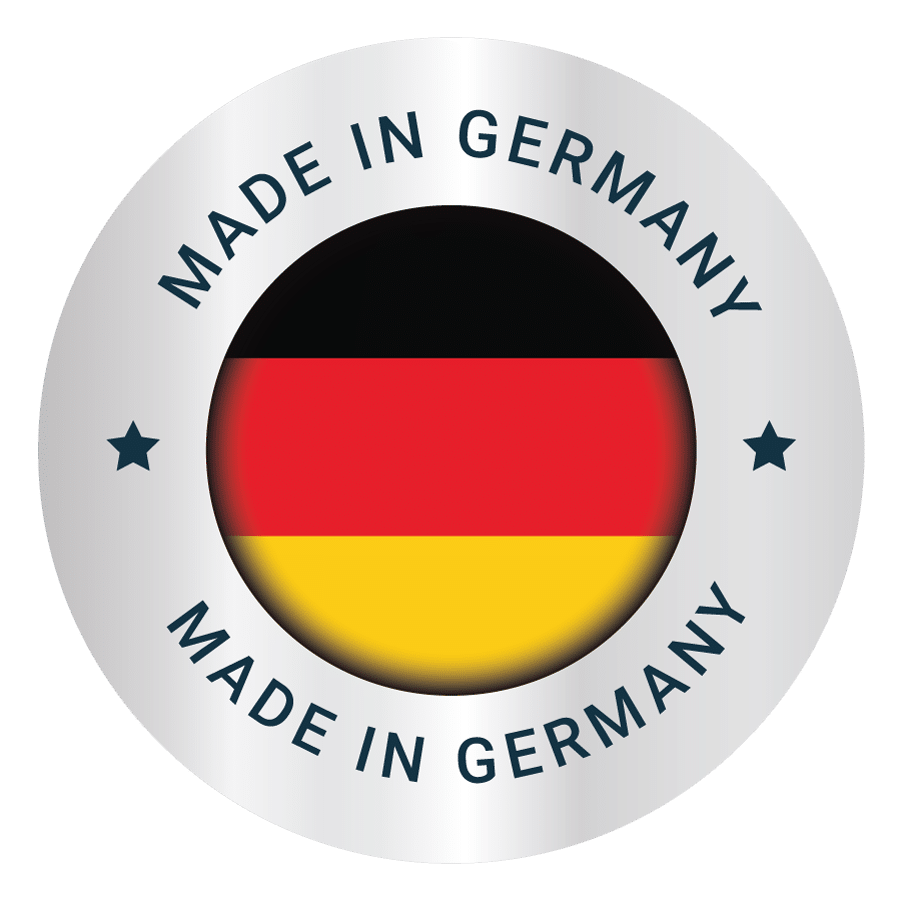
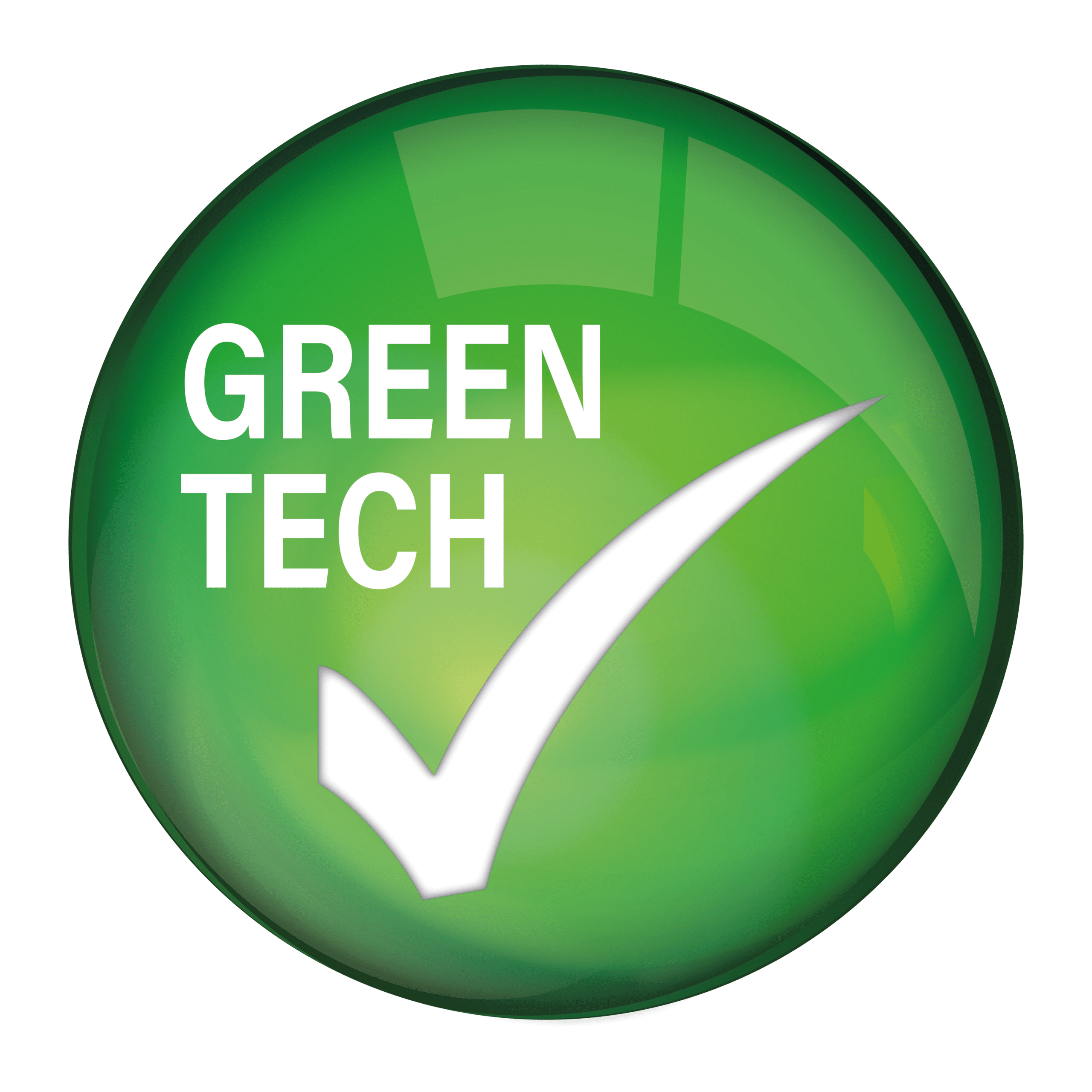
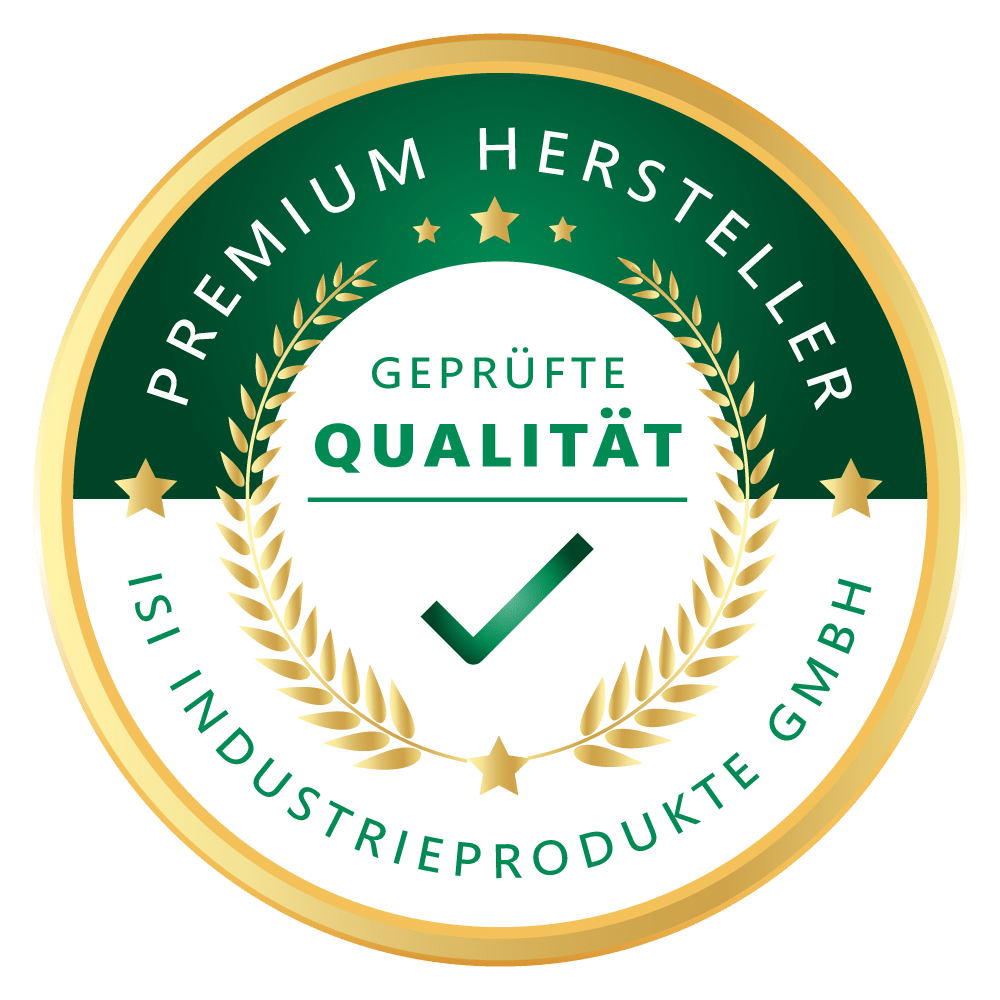
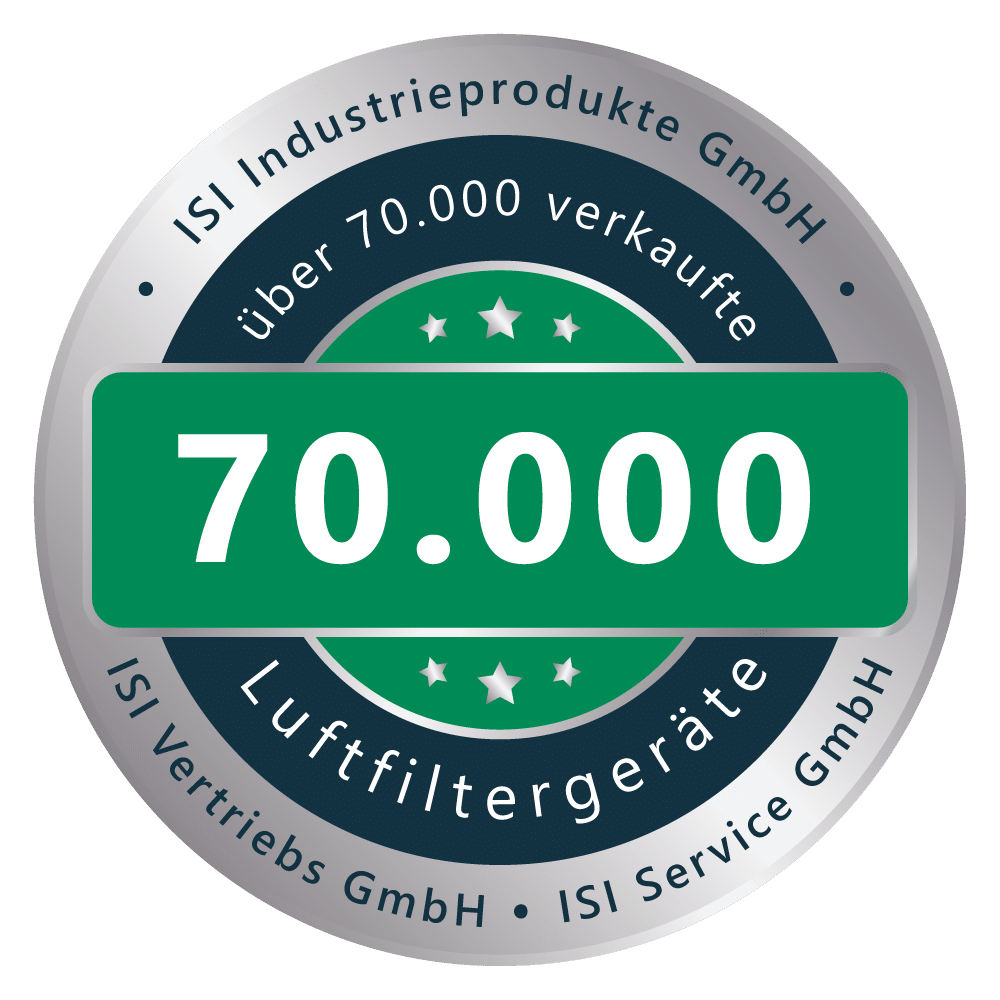
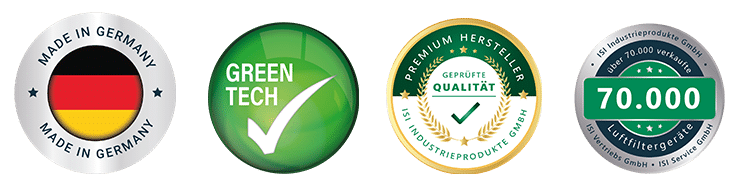
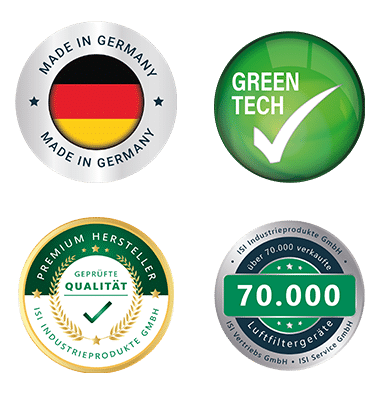
The ISI device series COBARON, TEBARON and ELBARON®
COBARON
Mechanical air filter units for the extraction of emulsion mist.
To the product
TEBARON
Mechanical air filter units for the extraction of emulsion mist.
To the product
ELBARON®
Electrostatic air filter device for extracting oil mist, emulsion mist and smoke.
To the product
ELBARON®
Electrostatic air filter system without fan for HVAC systems.
To the procuct